
New ISO standard at cyber-Wear
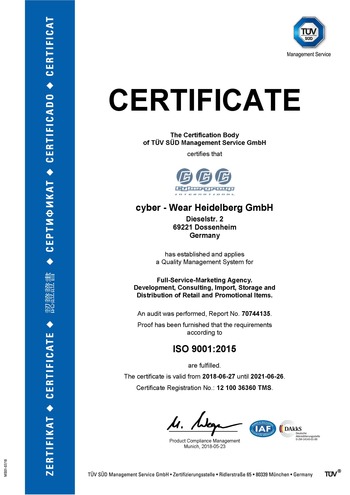
Last week all of cyber-Wear's operating processes came under the closest scrutiny. The reason for this was the TÜV audit for ISO 9001:2015 certification. In the following interview, cyber-Wear Quality Management Officer Anika Merkel provides details of the relevant facts, information and significance of the revised standard.
1. What is ISO 9001:2015?
Here in Germany and internationally, the ISO 9001 quality management standard is the most widespread and important standard in the quality management (QM) field. Certification in accordance with ISO 9001 is available to companies and organisations of all sizes and all sectors of the economy, and forms the basis for the continuous improvement process within the company's internal quality management system (QMS). ISO 9001 specifies the minimum requirements of a quality management system that need to be implemented by companies in order to fulfil customer requirements and further demands on the quality of their products and services. The introduction of a QM system enables companies, for example, to increase the transparency of their operating processes, generate greater customer satisfaction and reduce their error rate, which in turn brings down costs.
Process orientation is a fundamental principle of ISO 9001. A process-oriented QM system monitors all significant operating processes and puts them to the test. Even in the best organisations this can reveal optimisation possibilities. The latest version is DIN ISO 9001: 2015.
2. Is this based on an existing standard?
Yes, the last version was 9001:2008.
3. What changes are there between ISO 9001: 2008 and ISO 9001: 2015?
The previous standard concentrated more on manufacturing companies. In contrast, the new standard also explicitly focuses on service providers, including the commercial sector to which we belong. In addition the norm also has other focal points.
In the first case the process approach is to be applied and intensified more generally. The plan-do-check-act cycle for management-based thinking and action is to be pursued further.
"Risk-based thinking" is a further key term. In addition the specifications relating to documentation have been revised, and a management manual, for example, is no longer an essential.
4. Why was compliance with the norm only implemented in 2018, instead of in 2015?
Our certificate under the previous standard was still valid, and in 2017 the structure of our processes wasn't ready for the new version. The new audit was therefore the ideal opportunity to receive certification under the new standard.
5. What processes are audited?
Within our company the following processes are differentiated: management processes, core and support processes. By analysing the interaction among processes we can see what processes have an influence on one another. The main focus here is of course on our core processes. These are, for example, warehouse processes such as order picking, dispatch operations and incoming goods checks, as well as our entire order processing.
6. What personnel are involved?
The standard needs to cover the entire company. The TÜV accordingly looks at all departments and personnel that are part of a particular process. In practice this means our entire workforce.
7. How long does the audit take?
The full audit or a follow-up audit which we have now also had, takes two days. In the course of the next two years the TÜV will carry out a monitoring audit at our company, but this only takes one day.
8. What is the objective of the ISO 9001:2015 standard?
The prime objective and an important part of the standard is customer satisfaction, against which we measure ourselves in all areas. In addition we wish to achieve the quality targets we have set ourselves, to identify and accordingly avoid any calculable risks, and to define our opportunities. An effective quality management system also ensures healthy growth.
9. What does receipt of the certification mean for the future?
On the basis of this standard we can ensure transparency within our company and – because our processes are clearly visible – respond faster to changes on the market or within the industry. In addition our structures are also clarified.
10. What will change within the company as a result?
Looking back, the effect has been that we have been able to integrate new employees and customers correctly into our company structure by the application of the QMS. In order for a company to survive successfully on the market and grow, it needs clearly defined processes, communications guidelines, comprehensive documentation and effective management of all this information.
11. What does certification mean for the market?
Certification is a clear advantage on the market, because it confirms that an independent certification institution has occupied itself with us in detail, and has done so since 2009. They take a close look behind the scenes and scrutinise all processes individually. Customers know and notice this in everyday operations, too. Staff also find it easier to operate in clearly defined structures. In turn this ensures that we can always achieve a high level of customer satisfaction.